Safety
Here at Abra Cadabra Cleaning Services, we take safety seriously! Listed out are just some of the items we do to help our team and people around us stay safe. To view our full manual, click on the button below.
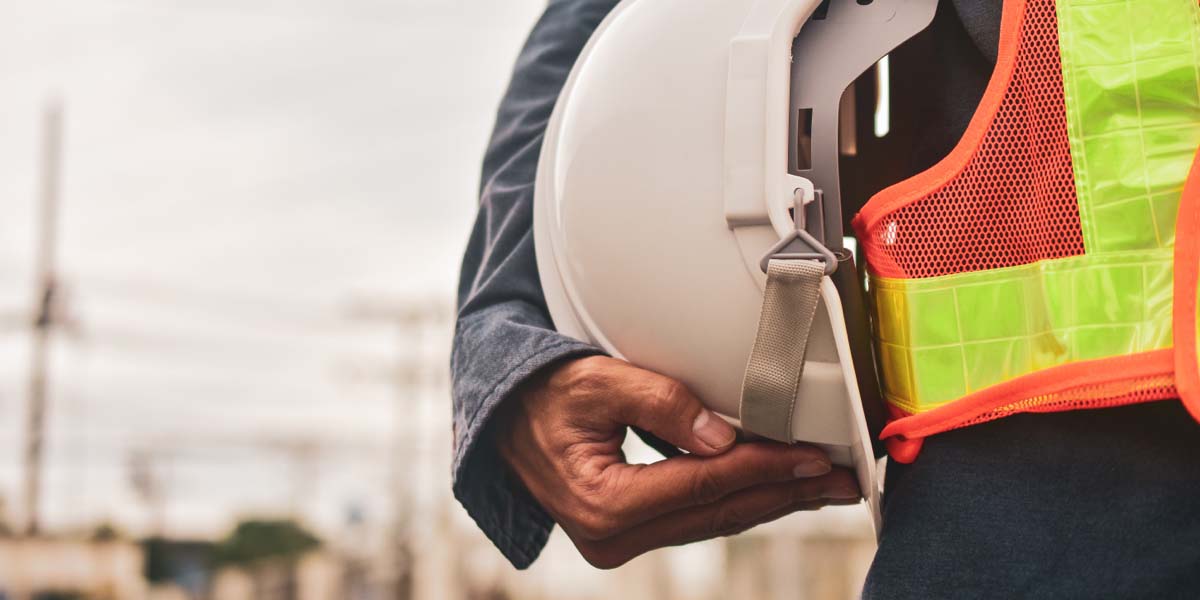
Training
Training is an essential component of an effective safety and health program, addressing the responsibilities of both management and employees in the workplace. Training is most effective when incorporated into other education on performance requirements and job practices.
Training programs are provided as follows:
- Initially, when the safety and health plan is developed or upgraded
- For all new employees, before beginning work
- When new equipment, materials, or processes are introduced
- When procedures have been updated or revised
- When incidents/accidents show that safety performance must be improved
Besides the standard training, employees should also be trained in the recognition of hazards – to be able to look at an operation and identify unsafe acts and conditions.
A list of typical hazards employees should be able to recognize may include:
- Fall Hazards: Fall exposures from ladders (straight and step) and any other surface more than 6 feet above the floor.
- Electrical Hazards; Damaged cords, outlets, overloads, extension cords, portable tools (broken casing or damaged wiring), grounding, metal boxes, switches, Ground Fault Circuit Interrupters(GFCI).
- Housekeeping Issues; Exits, walkways, floors, trash, storage of materials (Hazardous and Non-Hazardous), trips/slips, uneven flooring, etc.
- Fire Hazards; Oily-dirty Rags, combustibles, fuel gas cylinders, exits blocked, damaged electrical cords, etc.
- Health Hazards: Loss of hearing from noisy environments, and eye injury due to flying objects, etc.
Safety Meetings
Employees of Abra Cadabra Cleaning Service shall attend and participate in periodic safety meetings. The safety meeting shall be conducted by the Safety Coordinator. Safety problems that have arisen or that are anticipated shall be discussed along with any other work site or operations topics. The meeting shall be a valuable educational experience by:
- Keeping the meetings moving.
- Starting and stopping on time.
- Using illustrated material and demonstrations to make the point.
- Discussing each topic thoroughly, providing handouts if possible.
- Reviewing accidents, injuries, property losses, and “near misses”.
The Safety Coordinator must document the meetings using the appropriate form.
OSHA Log Review
In the event of a fatality (death on the job) or catastrophe (accident resulting in hospitalization of three or more workers), contact the Safety Coordinator, Nedal Anabtawi. The office phone number is (260) 490-6802.
The Safety Coordinator will, in turn, report it to the OSHA National Emergency Line at (800) 321-OSHA (6742) or the local Regional OSHA Office within 8 hours after the occurrence.
If an injury or accident should occur, employees are to report the injury to their Supervisor as soon as possible. A log entry and summary report shall be maintained for every recordable injury and illness. The entry should be done within 7 days after the injury or illness has occurred. The OSHA 300 or equivalent shall be used for the recording.
An OSHA recordable injury or illness is defined as an injury resulting in loss of consciousness, days away from work, days of restricted work, or medical treatment beyond first aid.
First Aid includes:
- Tetanus shots
- Band-aids or butterfly bandages
- Cleaning, flushing, or soaking wounds
- Ace bandages and wraps
- Non-prescription drugs at non-prescription strength (Aspirin, Tylenol, Etc.)
- Drilling fingernails/toenails
- Eye patches, eye flushing, and foreign body removal from the eye with Q-tips
- Finger guards
- Hot or cold packs
- Drinking fluids for heat stress
An annual summary of recordable injuries and illnesses must be posted at a conspicuous location in the workplace and contain the following information: Calendar year, company establishment name, establishment address, certifying signature, title, and date. If no injury or illness occurred in the year, zeroes must be entered on the total line at the bottom of the form.
The OSHA logs will be evaluated by management to determine trends or patterns in injuries to appropriately address hazards and implement prevention strategies.